Visual Inspection (VI), sometimes referred to as VIP in the pharmaceutical industry, is a critical quality control step used to ensure the drugs and their packaging meet predetermined standards.
Article content
What is inspected during Visual Inspection (VIP)?
Here are some of the key elements examined during a VIP in a pharmaceutical setting:
- Drugs: Inspectors will look for defects like discoloration, cracks, chips, or any foreign particles in the tablets, capsules, or other dosage forms.
- Packaging: Vials, bottles, blisters, labels, and other packaging components are checked for cracks, tears, leaks, or any printing errors on labels.
- Equipment: Manufacturing equipment used in drug production undergoes visual inspection to ensure there's no visible damage, wear and tear, or signs of contamination.
Why is Visual Inspection (VIP) important?
Visual Inspection plays a vital role in pharmaceutical quality control because it allows for the detection of potential issues that might be missed by automated inspection methods. Here's why it's important:
- Early detection of defects: VIP can catch problems early in the manufacturing process, preventing defective products from reaching patients.
- Ensuring product integrity: It helps ensure the drugs are packaged correctly and haven't been tampered with.
- Maintaining compliance: Proper visual inspection procedures are essential for complying with regulatory requirements set by agencies like the FDA.
Additional Points about VIP:
- Training: Inspectors for VIP undergo rigorous training to ensure they can effectively identify defects and differentiate between acceptable variations and rejections.
- Documentation: The findings of a visual inspection are typically documented in detail for traceability and audit purposes.
- Limitations: While valuable, VIP has limitations. It can't detect internal defects within a drug or contamination at the microscopic level.
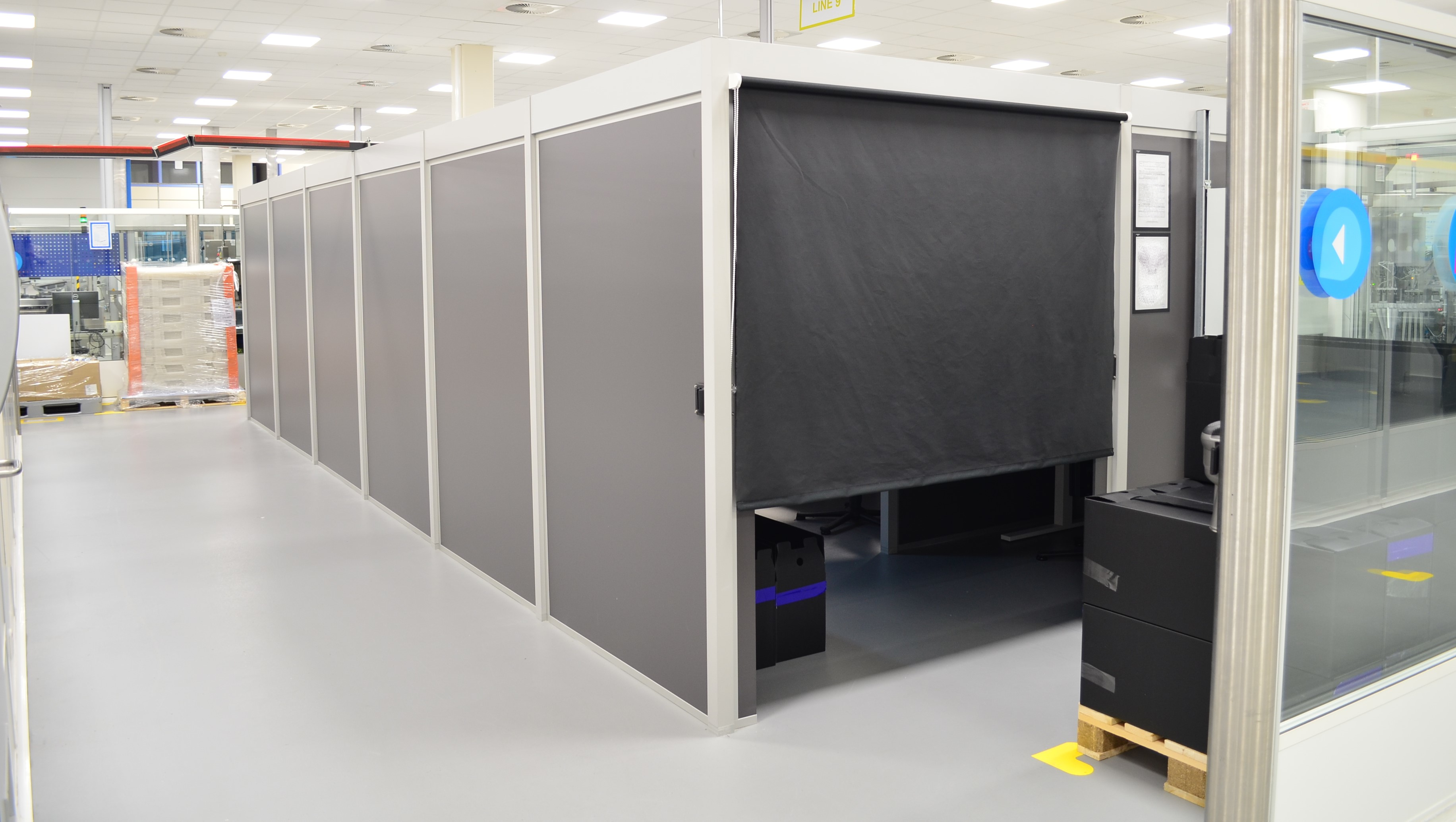
Facility Specifications
Lighting:
- Intensity: The light source should be bright enough for inspectors to clearly see the product but not cause glare.
- Color Temperature: A neutral color temperature (around 5,000 Kelvin) is preferred to avoid distorting the product's appearance.
- Uniformity: The light should be evenly distributed across the inspection area to prevent shadows or areas with poor visibility.
Background:
- Color: A neutral, non-distracting background is ideal, often dark or light grey, to provide contrast for the product being inspected.
- Cleanliness: The background surface should be clean and free of any debris or markings that could interfere with the inspection.
Magnification:
- Low-power magnification: For some inspections, inspectors might use magnifying lamps or loupes to examine details invisible to the naked eye.
- Training: Inspectors are trained on proper usage of magnification tools to ensure they don't damage the product or introduce errors.
Ergonomics:
- Adjustable workstation: The inspection area and the design of the cleanroom furniture should have a height-adjustable chair and workstation to promote proper posture and minimize fatigue for inspectors.
- Rest breaks: Regular rest breaks are crucial to prevent eye strain, fatigue, and ensure consistent inspection quality.
Additional Considerations:
- Calibration: Light sources and any magnification tools are regularly calibrated to ensure accuracy and consistency throughout the inspection process.
- Cleaning and disinfection: The inspection area, including tools and surfaces, is cleaned and disinfected regularly to prevent contamination.
- Documentation: The specific lighting, background, and other relevant conditions used during an inspection are documented for consistency and audit purposes.
By maintaining thesecontrolled conditions, pharmaceutical companies can ensure that visualinspections are conducted effectively and reliably, ultimately contributing tothe safety and quality of their products.
Innovative Facility Solutions:
At Kardeco, we understand the importance of providing optimal conditions for inspectors toperform their duties effectively. That's why we've collaborated with renowned operating pharmaceutical facilities in Belgium and partnered with Kupan's engineers to develop innovative solutions, such as building a lightbox. This lightbox, constructed from full core HPL (High-Pressure Laminate) phenolicpanels, isolates inspectors from the surrounding hall's light, ensuring that manual inspections are conducted with utmost precision and accuracy. Additionally, our expertise in cleanroom furniture ensures that the inspection environment maintains the highest standards of cleanliness and organization,further enhancing the reliability of inspection processes. By investing in such cutting-edge infrastructure, we contribute to enhancing the overall quality assurance process in the pharmaceutical industry, further solidifying our commitment to excellence and safety.