In the food and beverage processing industry, as well as pharmaceutical cleanrooms, maintaining a high standard of hygiene is an absolute must.
Article content
In the food and beverage processing industry, as well as pharmaceutical cleanrooms, maintaining a high standard of hygiene is an absolute must. This extends beyond the production floor to the changing rooms where employees transition between street clothes and work attire. Here at Kardeco, we understand the importance of hygienic design principles in creating a clean and safe environment for your staff.
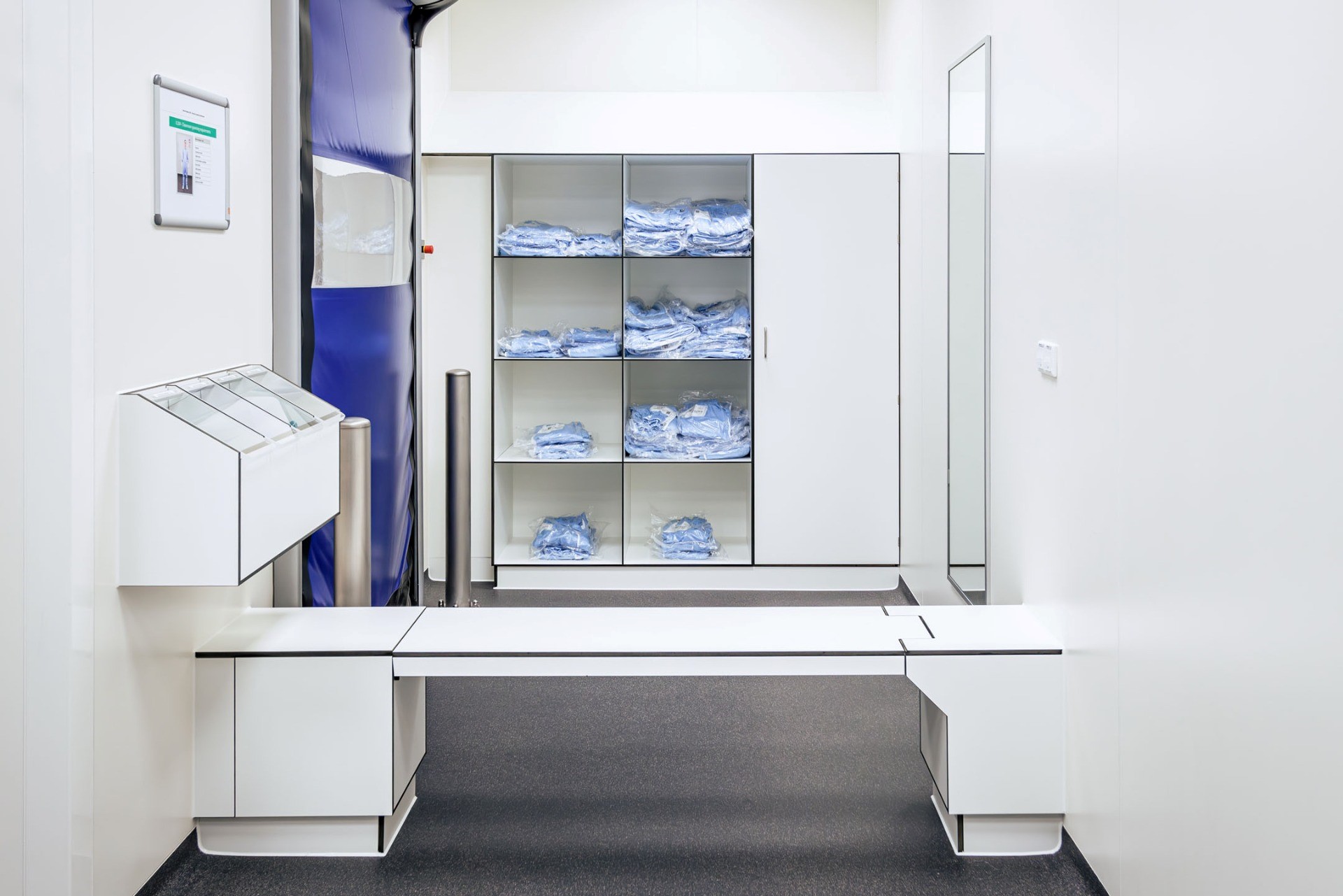
Prioritizing Hygiene in Changing Rooms
Contamination risks can lurk anywhere in a food and beverage processing facility or pharmaceutical cleanroom. By implementing a well-designed changing room, you can significantly reduce the potential for cross-contamination and ensure the safety of your products and your employees.
Key Considerations for Hygienic Design:
- Materials: Phenolic panels are your champion here. These non-porous panels are ideal for walls, partitions, lockers, and even countertops. Easy to clean and disinfect, they're crucial for preventing contamination. They're also moisture-resistant, withstanding the humidity and frequent cleaning routines common in these industries.
- Traffic Flow: Design your changing room with clear traffic flow in mind. Utilize phenolic partitions to separate "clean" and "street" areas. This simple step prevents cross-contamination between personal clothing and work attire.
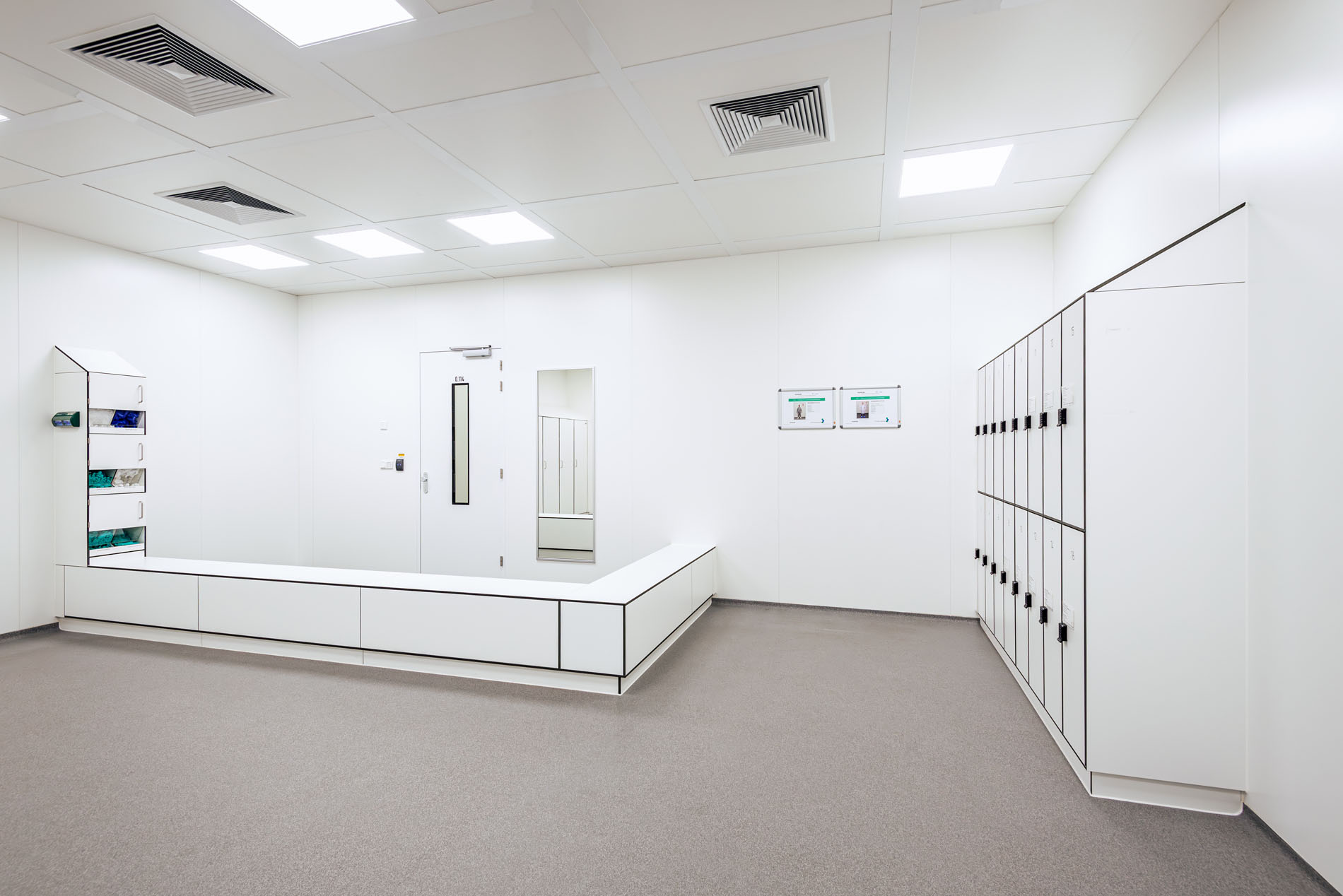
- Spaciousness: Don't cram employees in! Ample space between lockers and benches is key to preventing overcrowding and potential contact between employees. This not only promotes hygiene but also creates a more comfortable environment for your staff.
- Ventilation: Maintaining good ventilation is essential for removing moisture, odors, and airborne contaminants. Exhaust fans or natural ventilation systems are a must. In cleanroom settings, consider positive pressure ventilation to further minimize contamination risks.
- Fixtures and Equipment: Smooth surfaces are your friend! Phenolic panels are perfect for lockers, benches, and other fixtures. Their smooth surfaces are easy to clean and minimize the nooks and crannies where dirt and bacteria can accumulate.
- Hands-free options: Automatic faucets, soap dispensers, and toilet flushers are crucial to minimize touch-based germ transmission. In cleanroom settings, consider foot pedals or sensor-activated options for an extra layer of protection.
- Designated Storage: Provide separate areas for storing street clothes, work uniforms, and personal protective equipment (PPE). Utilize slatted shelves or hooks made from phenolic panels to allow for air circulation and drying of wet items. In cleanrooms, consider double-doored lockers or separate lockers for street clothes and PPE for maximum protection.
Kardeco: Your Partner in Hygienic Design
By following these hygienic design principles and incorporating top-quality materials like phenolic panels from Kardeco, you can create a changing room environment that promotes employee health and safety while minimizing contamination risks in your food and beverage processing or pharmaceutical facility. Contact Kardeco today to discuss your specific needs and create a hygienic changing room solution that works for you.
Committed to Industry Standards
As active members of EHEDG (European Hygienic Engineering & Design Group) and ISPE (International Society for Pharmaceutical Engineering), Kardeco is committed to providing solutions that meet the highest standards for hygiene and cleanability in the food & beverage and pharmaceutical industries.